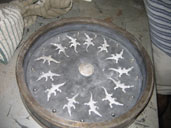 |
Mould Frame
Pewter figurines are cast
from hot metal using rubber moulds in a centrifugal casting machine.
The rubber moulds are made by placing a 12" rubber sheet
in the frame and laying out the master patterns around the mould
and placing another 12" rubber sheet on top. The frame is
then covered with a tight-fitting aluminium disc and placed in
the vulcaniser (below Left).
|
|
Casting Machine
Pewter figurines are cast
from hot metal using rubber moulds in a centrifugal casting machine.
Pouring Metal
|
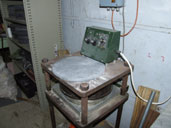 |
The Vulcaniser
The vulcaniser is a piece
of equipment designed to heat and pressurise the the mould frame
to cure rubber in the mould making process. The Vulcaniser consists
of two thermostatically controlled platens and a 20 tonne hydraulic
ram for closing the two platens onto the mould.
|
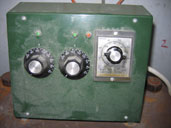 |
CONTROLS
The control panel consists
of two thermostatic controls and a timer.
Each platen has it's own
thermostat and these are set to 165º C.
The timer is adjustable
according to the thickness and size of the mould to be made.
|
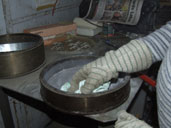 |
Making The Mould
The mould frame should
be powered with talcum powder to prevent the rubber from sticking
to the mould frame.
|
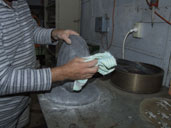 |
Making The Mould
Two disks of rubber about
12mm in thickness are then powdered with Talcum Powder to prevent
the two disks from sticking together when the rubber is vulcanised.
It will also allow for the removal of the master patterns when
the mould is made.
|
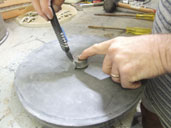 |
Making The Mould
One rubber disk has to
have a hole to allow the pewter to be poured into the finished
mould.
The centre is marked out.
|
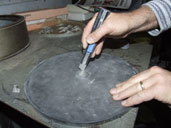 |
Making The Mould
The raw rubber is cut with
sharp knives.
|
 |
Making The Mould
The rubber is very pliable
before being cured and may be easily cut.
|
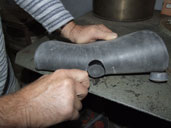 |
Making The Mould
The centre is removed and
the aluminium plug (right in picture) will be inserted in the
hole.
|
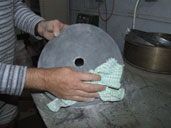 |
Making The Mould
The rubber is then coated
with talcum powder again.
|
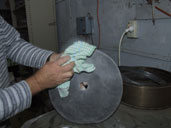 |
Making The Mould
Care should be taken to
ensure that the rubber is well coated with talcum powder.
|
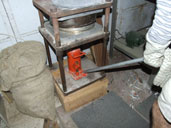 |
Making The Mould
The mould frame has been placed in the vulcaniser for an hour to
be pre-heated to about 160º
C. All the aluminium filler plates
are also heated.
|
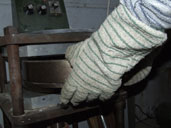 |
Making The Mould
The mould frame is removed from the vulcaniser using insulated
gloves.
|
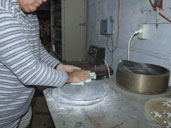 |
Making The Mould
The filler plates are also
coated with talcum powder. Whilst the bottom rubber disk is being
warmed.
|
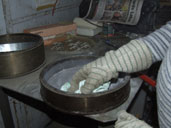 |
Making The Mould
The mould frame is again powdered ready for the first rubber disk
to be inserted
|
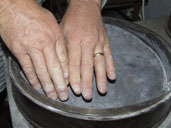 |
Making The Mould
The warm rubber disk is
pressed into the mould frame by hand.
|
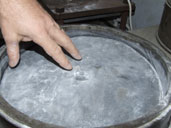 |
Making The Mould
The rubber is again powdered.
|
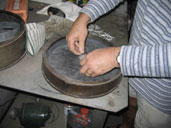 |
Making The Mould
The centre plug is powdered
and inserted in to the hole.
|
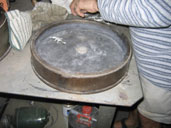 |
Making The Mould
The figurines are then
placed on the rubber towards the outer edge of the mould and
about 18 mm in from the mould frame perimeter.
|
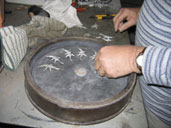 |
Making The Mould
even spacing is essential
to ensure a balanced mould when it is spun in the casting machine.
|
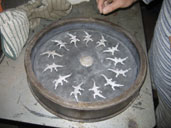 |
Making The Mould
The rubber in the mould
frame will be the top half of the mould and whilst the figurines
are place on this rubber the other rubber is being warmed.
|
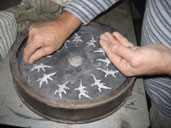 |
Making The Mould
Once the figurines are
in place locaters are placed between each of the figurines. This
is necessary to ensure that the top and bottom parts of the mould
always fit together.
|
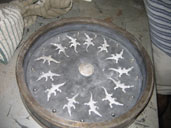 |
Making The Mould
The locators are now in
place with plenty of space between the outer edge of the mould.
|
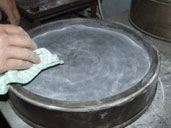 |
Making The Mould
The second rubber disk
is then pressed carefully into place so as not to disturb the
placement of the master patterns and powdered.
|
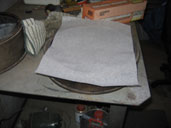 |
Making The Mould
A sheet of release paper
is placed over the top of the mould to ensure that the rubber
does not stick to the filler sheets.
|
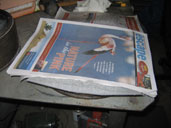 |
Making The Mould
About 8 - 10 sheets of newspaper are then
placed over the top of the mould frame to ensure a tight fit
which will not allow the rubber to seep out from the frame when
heated and under great pressure.
|
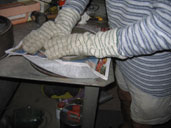 |
Making The Mould
An aluminium plate is the
carefully pushed into the frame so as not to disturb the placement
of the master patterns.
|
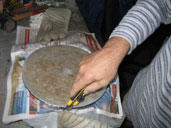 |
Making The Mould
Once the first aluminium
plate is in place, the excess newspaper is cut away using the
outer edge of the mould frame as a guide.
|
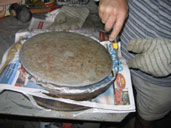 |
Making The Mould
A second filler plate is
in place and the paper is cut away.
|
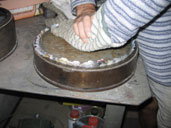 |
Making The Mould
The second filler plate
is carefully pushed into the frame.
|
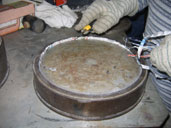 |
Making The Mould
Any
excess paper is then cut away.
|
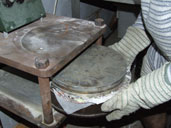 |
Making The Mould
The vulcaniser is still
at 160º C and the frame is then placed in between the vulcaniser
platens.
|
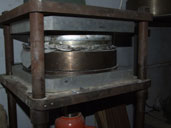 |
Making The Mould
The frame is always placed
in the centre of the platens to ensure that an even pressure
is exerted to ensure that the mould will be parallel.
|
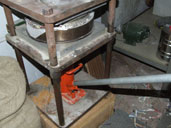 |
Making The Mould
The bottom platen is then
slowly jacked up to full pressure to ensure that the rubber is
squeezed around the figurines and into all the undercuts.
|
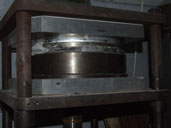 |
Making The Mould
The vulcaniser is at 160º
C and the frame starts to heat quickly.
|
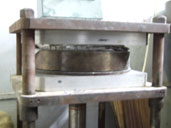 |
Making The Mould
The frame is now under
full pressure and the timer is set for two hours.
|
Removing the mould
Pictures Coming
|
Making The Mould
After two hours, the pressure
is released on the platens and the mould frame is removed from
the vulcaniser.
|
Cutting In The Mould
Pictures Coming
|
The mould is removed from the frame
and excess rubber is cut from the perimeter of the cured mould.
The mould is nicked on the top
and bottom to easily identify the position of the two halves.
The mould is opened and the figurines
are carefully removed. These figurines are the master patterns
and will be saved for later use when new moulds are required.
|
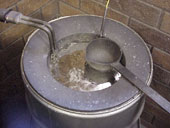 |
The Melting
Pot.
The melting pot is used
to melt bars of pewter. It holds over 60 Kgs. of metal. The temperature
of the metal is measured with a thermo couple and a thermostat
controls the metal temperature within a few degrees.
Pewter is cast at between
290º C and 320º C depending on the bulk of the pieces
being cast. The ladel will hold about 2 kgs of metal.
|
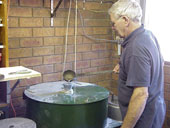 |
Casting Machine
The mould is placed in the casting machine.
and a top plate is located and secured on top of the mould.
The lid of the casting machine is closed
and the mould begins to spin. When it has reached the correct
speed, molten pewter is poured into the mould.
|
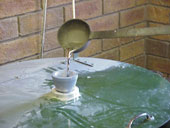 |
Casting Machine
The metal is poured carefully and continuously
to ensure that the mould is filled and care is taken so as not
to overfill the mould.
|
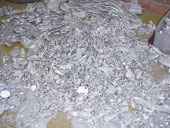 |
Pewter Figurines
Once the figurines are cast, they have
to be detailed.
|
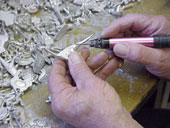 |
Detailing Figurines
A high speed drill with tungsten carbide
bits is used to detail the figurines. The drill is similar to
a dentist drill and as powered by compressed air. High speed
steel bits can also be used.
|
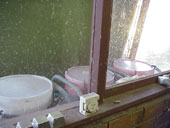 |
Polishing Figurines
Once the figurines are detailed they are
polished in large vibrating tumblers using a technique developed
by this company.
|
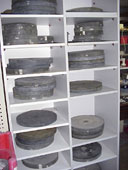 |
Rubber Moulds
Rubber moulds can be used over and over
again and providing care is taken, they will last for well over
100 spins.
|